Als hoogwaardig materiaal wordt aluminiumoxidesubstraat op grote schaal gebruikt in de elektronica, de ruimtevaart en nieuwe energievelden. Het voorbereidingsproces omvat veel ingewikkelde processen, waarbij het giet- en droogproces de belangrijkste schakels zijn om de kwaliteit van het substraat te garanderen. In dit artikel werden de effecten van de grondstofformule, de gietfilmdikte en de parameters van het sinterproces op de eigenschappen van keramisch aluminiumoxide-substraat onderzocht, en werden het droogproces na het gieten en het mechanisme ervan op de kwaliteit van het substraat geanalyseerd.
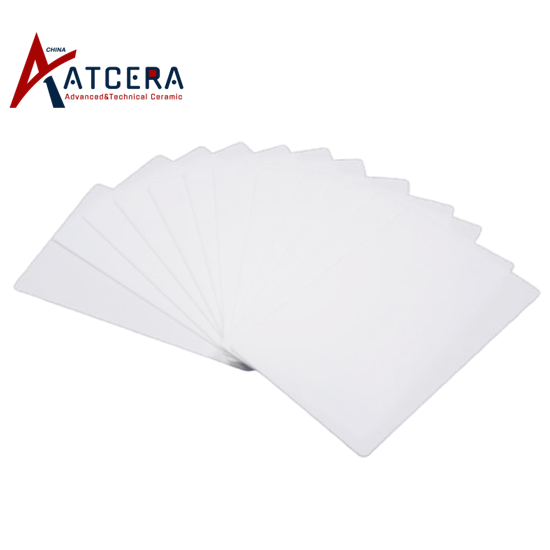
Grondstofformule en controle van de gietfilmdikte:
De uiteindelijke dikte en dikte-uniformiteit van keramisch aluminiumoxide-substraat worden rechtstreeks beïnvloed door de precieze verhouding tussen de formulering van de grondstof en de juiste dikte van de gegoten filmstrip. Een redelijke verhouding grondstoffen draagt bij aan de vorming van een stabiele gietmassa en de keuze van de filmdikte bepaalt de initiële vorm van de groenstrook, die mede de basiskwaliteit van het substraat bepaalt.
Invloed van parameters van het sinterproces:
Het onthechten van sinteren is een belangrijke stap bij de voorbereiding van het substraat, en de procesparameters ervan, zoals temperatuur en tijd, hebben rechtstreeks invloed op de kwaliteit van het uiterlijk en de oppervlakteruwheid van het substraat. Het optimaliseren van deze parameters kan de algehele prestaties van het substraat aanzienlijk verbeteren, zoals het vergroten van de sterkte en het verminderen van de porositeit.
Belang van het droogproces en gefaseerde implementatie:
Vanwege de hoge viscositeitseigenschappen van de gegoten slurry is het droogproces de sleutel om de sterkte en het volledige strippen van de groene strip te garanderen. Tijdens het droogproces vereisen de productie en het vrijkomen van de interne spanning van het groene vel en de onbalans van het soortelijk gewicht veroorzaakt door de vervluchtiging van het oplosmiddel de formulering van een nauwkeurig droogproces. De droogfase met constante snelheid heeft tot doel de vloeistoffasefilm snel op het oppervlak te verdampen, terwijl de droogfase met lagere snelheid zich richt op de langzame diffusie van het interne oplosmiddel om de drooguniformiteit te garanderen en defecten zoals scheuren en kromtrekken te voorkomen.
Specifieke analyse van het droogproces:
Omdat de verdampingssnelheid van de vloeibare film op het oppervlak veel hoger is dan de diffusiesnelheid van het oplosmiddel binnenin, moet het droogproces van groene strip in fasen worden uitgevoerd. In de constante droogfase is de droogsnelheid constant, wat overeenkomt met de verdampingssnelheid van het oppervlakteoplosmiddel, en wordt de oppervlaktevloeistoffasefilm hoofdzakelijk verwijderd. Wanneer het drogen van het oppervlak is voltooid, gaat het naar de droogfase met verlaagde snelheid en wordt de droogsnelheid geleidelijk verlaagd om zich aan te passen aan de snelheid van de interne diffusie van het oplosmiddel naar het oppervlak, waardoor de uniformiteit en stabiliteit van het droogproces wordt gegarandeerd.
Samenvattend vereist het bereidingsproces van keramisch substraat van aluminiumoxide een strikte controle van de grondstofformule, de dikte van de gegoten film en de parameters van het sinterproces voor het ontviscosificeren. Als belangrijke stap is de nauwkeurige implementatie van het droogproces cruciaal om de uniformiteit van de dikte, de kwaliteit van het uiterlijk en de oppervlakteruwheid van het substraat en andere indicatoren voor technische toepassingen te garanderen. Door het drogen met constante snelheid en verminderde snelheid in verschillende fasen te implementeren, kan de spanningsverandering in de groene plaat effectief worden gecontroleerd en kunnen droogfouten worden vermeden, wat een sterke garantie biedt voor de bereiding van hoogwaardig aluminiumoxide-keramisch substraat. In de toekomst, met de voortdurende vooruitgang van de materiaalwetenschap en voorbereidingstechnologie, zal het voorbereidingsproces van keramisch aluminiumoxide-substraat verfijnder en intelligenter zijn, waardoor een hoogwaardigere materiaalbasis wordt geboden voor toepassingen op verschillende gebieden.