Met de voortdurende evolutie van de micro-elektronische verpakkingstechnologie is de vermogensdichtheid van elektronische componenten aanzienlijk toegenomen, wat heeft geresulteerd in een scherpe toename van de warmteontwikkeling per volume-eenheid, wat strengere normen heeft opgeleverd voor de prestaties van de nieuwe generatie printplaten in termen van van de efficiëntie van de warmteafvoer (thermische geleidbaarheid). Momenteel onderzoeken en ontwikkelen onderzoekers actief verschillende keramische substraatmaterialen met een hoge thermische geleidbaarheid, waaronder aluminiumnitride (AlN), siliciumcarbide (SiC) en berylliumoxide (BeO ). BEO's zijn echter vanuit milieuoogpunt beperkt vanwege hun potentiële toxiciteit; SiC wordt vanwege de hoge diëlektrische constante niet als een ideaal substraatmateriaal beschouwd. Daarentegen is AlN een spraakmakende keuze voor substraatmaterialen geworden vanwege de vergelijkbare thermische uitzettingscoëfficiënt als silicium (Si) en de gematigde diëlektrische constante-eigenschappen.
Traditioneel zijn dikkefilmslurries voornamelijk ontwikkeld op basis van aluminiumoxide (Al2O3)-substraten, maar de componenten van deze slurries zijn gevoelig voor chemische reacties wanneer ze in contact komen met AlN-substraten en produceren gas, wat een ernstige bedreiging vormt voor de stabiliteit en prestaties van dikke films. filmcircuits. Omdat de thermische uitzettingscoëfficiënt van het AlN-substraat lager is dan die van het Al2O3-substraat, zal het directe gebruik van het slurry- en sinterproces dat is ontworpen voor Al2O3 op het AlN-substraat bovendien leiden tot een mismatch van de thermische uitzetting, wat problemen zal veroorzaken. Daarom is het niet raadzaam om het materiaalsysteem en het productieproces dat van toepassing is op het Al2O3-substraat eenvoudigweg te transplanteren naar het AlN-substraat. Dit artikel richt zich op het fabricageproces van weerstanden op AlN-substraat, bespreekt het fabricageproces diepgaand en evalueert en analyseert de prestaties van weerstanden in detail.
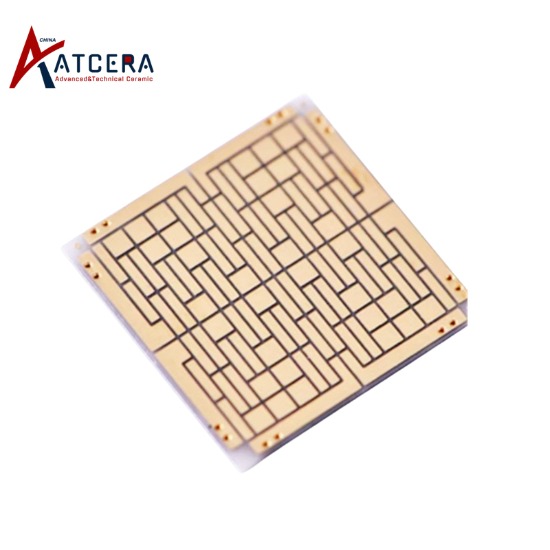
weerstandsontwerpnummer
Om de relatie tussen de weerstandswaarde van het AlN-substraat en het aantal ontwerpvierkanten te bepalen, werd de weerstandstestplaat ontworpen (zoals weergegeven in figuur 4). De lengte van de weerstand varieert van 500 tot 2000 μm en de breedte varieert van 500 tot 2500 μm. De weerstanden met vier soorten vierkante weerstand werden op het AlN-substraat gedrukt en de film werd gesinterd bij 850ºC, en de weerstandswaarden van de weerstanden met verschillende ontwerpgroottes werden gemeten.
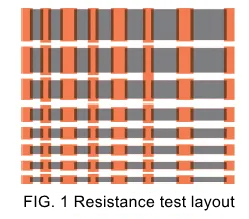
De weerstandswaarde van drie substraten van dezelfde grootte wordt gemeten, het vierkante ontwerpgetal van de maatweerstand wordt berekend, de weerstandswaarde van de drie weerstanden wordt gemiddeld en de relatie tussen de weerstandswaarde en het vierkante getal van de Er worden vier soorten vierkante weerstand gevormd (zoals weergegeven in figuur 2).
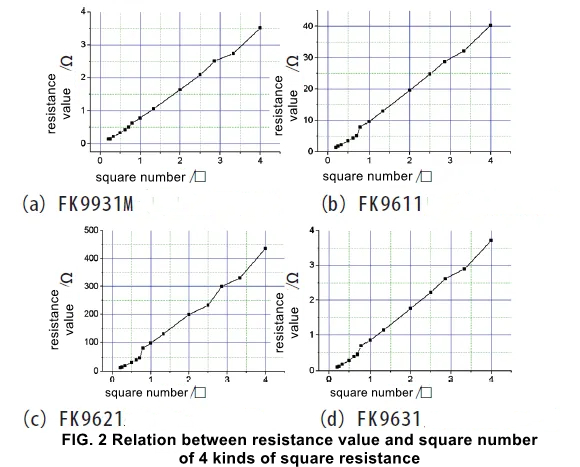
Wanneer de initiële waarde van de weerstandsafdruk in het algemeen wordt ontworpen om 80% van de nominale waarde te zijn, is dit het meest bevorderlijk voor de verbetering van de aanpassingswaarde en de opbrengst. Gecombineerd met het relatiediagram tussen de weerstandswaarde en het kwadratische getal wordt het ontwerpaandeel van de vier vierkante weerstanden berekend (zie Tabel 1).
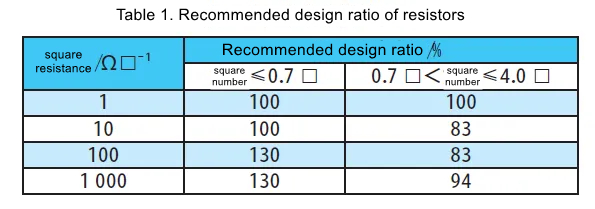
Proces voor aanpassing van de weerstandswaarde
Bij de daadwerkelijke productie van dikke filmweerstand kan de fout tussen de weerstandswaarde en de doelwaarde, zelfs als de slurrysamenstelling, het drukproces, de filmdikte, het bakken en de afstemming van de elektroden strikt worden gecontroleerd, slechts ± 20% bedragen. Om op basis van de gemaakte dikkefilmweerstand de weerstandswaarde met de vereiste nauwkeurigheid te verkrijgen, kan de waarde alleen aangepast worden. In termen van het verbeteren van de nauwkeurigheid van de vloei- en weerstandswaarde is waardeaanpassing een essentiële en belangrijke technologie.
De procesparameters van weerstandsaanpassing op AlN-substraat zijn als volgt: stroom 14,5 A, Q-frequentie 2500 Hz, laserpuntafstand 150. Gebaseerd op de analyse van de vorm van de snijmarkeringen na aanpassing, de breedte van de weerstandssnedemarkeringen van de vier soorten vierkante weerstand is groter dan 30 μm, en er is geen weerstand en substraatresten in de snijmarkeringen, wat voldoet aan de relevante vereisten van de inspectiedocumenten.
Samenvattend: met de snelle ontwikkeling van de micro-elektronische verpakkingstechnologie nemen de eisen aan de warmtedissipatie-efficiëntie van de circuitplaat toe, wat het onderzoek en de ontwikkeling van keramische substraatmaterialen met een hoge thermische geleidbaarheid bevordert. Onder hen onderscheidt aluminiumnitride (AlN) zich van veel kandidaat-materialen vanwege zijn superieure thermische uitzettingsaanpassing en gematigde diëlektrische constante-eigenschappen, en is het een populaire keuze geworden voor een nieuwe generatie printplaatmaterialen. Het unieke karakter van het AlN-substraat vereist echter ook dat we overeenkomstige aanpassingen en optimalisaties doorvoeren in de selectie van dikkefilmslurry en het productieproces om de problemen te vermijden die worden veroorzaakt door hetzelfde materiaalsysteem en proces als het Al2O3-substraat.
Door de weerstandstestplaat te ontwerpen, de relatie tussen weerstand en kwadraat te meten en te analyseren, en de weerstandsaanpassingstechnologie te onderzoeken, wordt de weerstandsproductietechnologie op AlN-substraat in dit artikel diepgaand bestudeerd. De resultaten laten zien dat de weerstand met stabiele prestaties en hoge precisie kan worden gemaakt op AlN-substraat door de grootteverhouding van de weerstand redelijk te ontwerpen en de procesparameters nauwkeurig te controleren. Deze onderzoeksresultaten bieden niet alleen technische ondersteuning voor de toepassing van AlN-substraat op het gebied van micro-elektronica-verpakkingen, maar bieden ook een effectieve oplossing voor het warmtedissipatieprobleem van elektronische componenten met hoge vermogensdichtheid in de toekomst. Met de voortdurende vooruitgang van de technologie zal de verbetering van het AlN-substraat en het ondersteunende productieproces een nieuwe vitaliteit geven aan de duurzame ontwikkeling van de micro-elektronica-industrie.