Met de voortdurende vooruitgang van de micro-elektronische verpakkingstechnologie zijn de kracht en de integratie van elektronische componenten aanzienlijk toegenomen, wat heeft geleid tot een aanzienlijke toename van de warmteopwekking per volume-eenheid, waardoor strengere eisen zijn gesteld aan de efficiëntie van de warmteafvoer (dat wil zeggen , de warmtegeleidingsprestaties) van de nieuwe generatie printplaten. Momenteel werken onderzoekers aan de ontwikkeling van een verscheidenheid aan keramische substraatmaterialen met een hoge thermische geleidbaarheid, waaronder aluminiumnitride (AlN), siliciumcarbide (SiC) en berylliumoxide ( BeO). BeO is echter vanuit het milieu beperkt vanwege zijn toxiciteit; SiC is niet geschikt voor gebruik als substraatmateriaal vanwege de hoge diëlektrische constante-eigenschappen. Daarentegen is AlN het substraatmateriaal dat de voorkeur heeft vanwege de vergelijkbare thermische uitzettingscoëfficiënt en matige diëlektrische constante als silicium (Si) materialen.
Traditioneel zijn dikkefilmslurps voornamelijk ontworpen voor aluminiumoxide (Al2O3) substraten, maar de samenstelling van deze slurps is gevoelig voor chemische reacties bij contact met AlN-substraten, waarbij gassen worden geproduceerd die een ernstige bedreiging vormen voor de stabiliteit en prestaties van dikkefilmcircuits. Omdat de thermische uitzettingscoëfficiënt van het AlN-substraat lager is dan die van het Al2O3-substraat, zal het rechtstreeks toepassen van het slurry- en sinterproces dat geschikt is voor het Al2O3-substraat op het AlN-substraat bovendien leiden tot het probleem van de thermische uitzettingsmismatch, wat zal leiden tot invloed hebben op de prestaties van het circuit. Daarom is het niet raadzaam om het materiaalsysteem en het productieproces van het Al2O3-substraat eenvoudigweg te kopiëren naar het AlN-substraat. Dit artikel beschrijft in detail het fabricageproces van de weerstand ontworpen voor AlN-substraat, en bestudeert en analyseert de prestaties van de weerstand.
Meting van de weerstandstemperatuurcoëfficiënt
De weerstandstemperatuurcoëfficiënt (TCR) vertegenwoordigt de relatieve verandering van de DC-weerstandswaarde van de weerstand bij de testtemperatuur ten opzichte van de DC-weerstandswaarde bij de referentietemperatuur, dat wil zeggen de relatieve verandering van de weerstandswaarde ΔTCR voor elke temperatuur van 1 ° C tussen de testtemperatuur en de referentietemperatuur:
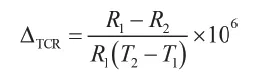
Waarbij: R1 de weerstandswaarde is bij de referentietemperatuur; R2 is de weerstandswaarde bij de testtemperatuur. T1 is de referentietemperatuur; T2 is de testtemperatuur.
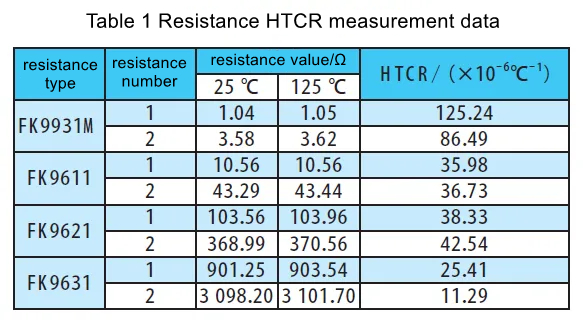
De dikkefilmweerstand op het AlN-substraat werd gemeten met TCR. De testgegevens bij hoge temperatuur-temperatuurcoëfficiënt (HTCR) zijn weergegeven in Tabel 1, en de testgegevens bij lage temperatuur-temperatuurcoëfficiënt (CTCR) zijn weergegeven in Tabel 2. Uit de testgegevens blijkt dat de ontwerpgrootte een bepaald effect heeft op de temperatuurcoëfficiënt van de weerstand. Alle weerstandsmodellen hebben een positieve temperatuurcoëfficiënt op dit AlN-substraat, en de TCR van FK9931M is minder dan 150×10-6/â, en de overige modellen zijn minder dan 100×10-6/â.
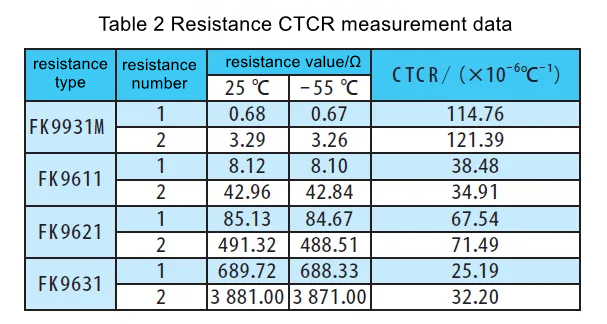
beoordeling van weerstandsstabiliteit
Weerstand kan worden beschouwd als een driedimensionale netwerkstructuur die is samengesteld uit vele geleidende ketens. Wanneer de weerstandslaag onder spanning komt te staan, zal de kwetsbaardere geleidende ketting breken of plaatselijk uitrekken, waardoor het totale geleidende vermogen afneemt en de weerstandswaarde toeneemt. Omgekeerd, wanneer de thermische uitzettingscoëfficiënt van de weerstandslaag duidelijk kleiner is dan die van het substraat, is de spanning binnen de weerstandslaag druk. Wanneer de weerstandslaag aan druk wordt blootgesteld, zal het contact tussen de deeltjes nauwer zijn en zal er zelfs een nieuwe geleidende keten worden toegevoegd, waardoor het geleidende vermogen van de gehele dikkefilmweerstand wordt verbeterd, en de weerstandswaarde zal worden verlaagd op de macro niveau. Omdat de dikkefilmweerstand stevig aan het substraat is gebonden en de spanningsafgifte langzaam is, zal de weerstandswaarde veranderen wanneer de dikkefilmweerstand bij een bepaalde temperatuur wordt bewaard. Hoe groter het verschil tussen de thermische uitzettingscoëfficiënt van de dikke-filmweerstand en het substraat, hoe groter de spanning binnen de dikke-filmweerstand, en hoe groter de veranderingssnelheid van de dikke-filmweerstand bij opslag bij hoge temperatuur.
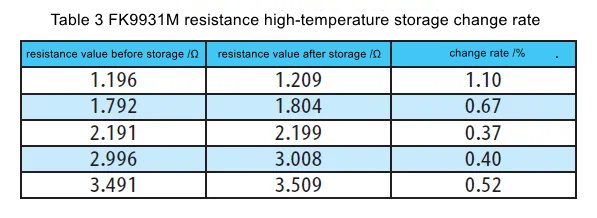
Volgens verschillende ontwerpgroottes werden vier soorten vierkante weerstandsweerstanden op het AlN-substraat gedrukt en werden de weerstanden aangepast met een laser. Na temperatuuropslag bij 150ºC en 1000 uur werd de verandering van de weerstandswaarden voor en na temperatuuropslag vergeleken. De weerstand van elke vierkante weerstand meet de weerstandswaarde van vijf weerstanden. Zoals uit Tabel 4 tot Tabel 6 blijkt, bedraagt de veranderingssnelheid van de weerstandswaarde minder dan 1,5% na opslag bij hoge temperatuur.

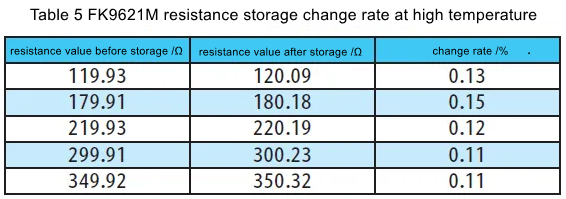
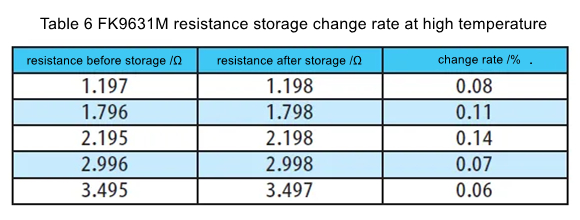
Samenvattend kunnen we stellen dat met de snelle ontwikkeling van de micro-elektronische verpakkingstechnologie de kracht en de integratie van elektronische componenten een kwalitatieve sprong voorwaarts hebben gemaakt, maar ook ongekende uitdagingen hebben opgeleverd voor de efficiëntie van de warmteafvoer van de printplaat. Onderzoekers hebben actief op deze uitdaging gereageerd door een reeks keramische substraatmaterialen met een hoge thermische geleidbaarheid te onderzoeken en te ontwikkelen, waaronder aluminiumnitride (AlN) dat zich onderscheidt van vele kandidaat-materialen met zijn superieure thermische uitzettingsaanpassing en gematigde diëlektrische constante. focus van huidig onderzoek.
In dit artikel worden de beperkingen van de traditionele dikkefilmslurry bij de toepassing van AlN-substraat diepgaand geanalyseerd en wordt het weerstandsproductieproces dat is ontworpen voor de kenmerken van AlN-substraat in detail beschreven. De experimentele resultaten laten zien dat de dikkefilmweerstand op AlN-substraat stabiele prestaties heeft, de temperatuurcoëfficiënt binnen het acceptabele bereik ligt en de weerstandsveranderingssnelheid zeer klein is na opslag bij hoge temperatuur, wat de haalbaarheid en effectiviteit van het productieproces verifieert. 53>
<54> <55>
<56>In de toekomst, met het verdere onderzoek en de optimalisatie van het AlN-substraat en het ondersteunende productieproces, hebben we reden om aan te nemen dat het AlN-substraat een belangrijkere rol zal spelen bij het verpakken van elektronische componenten met een hoge vermogensdichtheid, en de ontwikkeling van de micro-elektronica-industrie naar betere prestaties en hogere integratie bevorderen.<57>