Met de voortdurende vooruitgang van de halfgeleidertechnologie heeft siliciumcarbide (SiC), als hoogwaardig materiaal, een groot toepassingspotentieel getoond op het gebied van vermogenselektronische apparaten. Bij het voorbereidingsproces van siliciumcarbidesubstraat is de controle van de oppervlaktekwaliteit echter bijzonder cruciaal, vooral na het verdunnen, slijpen en polijsten en andere processen om een ultraglad oppervlak te verkrijgen. Onder hen is chemisch mechanisch polijsten (CMP), als een van de belangrijkste stappen, van groot belang voor het verwijderen van de beschadigde laag die is achtergelaten door het vorige proces en het bereiken van een hoge oppervlakte-egalisatie. Het traditionele CMP-proces wordt echter geconfronteerd met het probleem van een lage materiaalverwijderingssnelheid (MRR), wat een directe invloed heeft op de productie-efficiëntie en -kosten. Daarom is het verkennen van nieuwe technologieën om de CMP-efficiëntie van SiC-substraten te verbeteren de focus geworden van het huidige onderzoek.
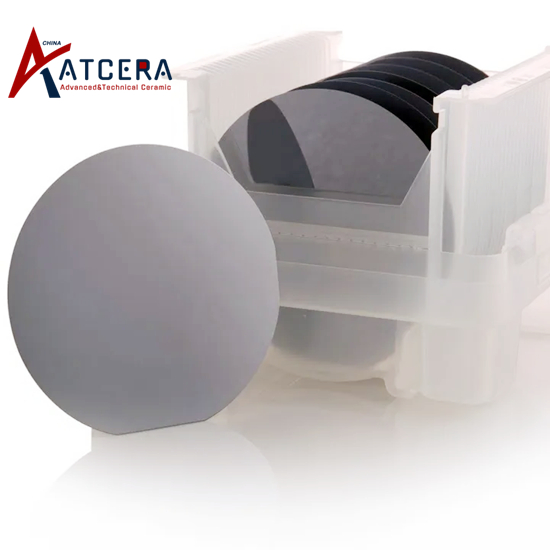
1. Basisprincipes en uitdagingen van SiC-substraat CMP
De oppervlakteschadediepte van het verdunde of gemalen SiC-substraat bedraagt gewoonlijk 2-5 μm en vereist verdere behandeling door CMP.
CMP-technologie is gebaseerd op het "chemische + mechanische" composietprincipe, door de combinatie van oxidelaagvorming en mechanische verwijdering, om een gladder oppervlak te bereiken.
2. Lage MRR is het grootste probleem van SiC-substraat CMP, en de CMP-efficiëntie van SiC is aanzienlijk lager dan die van siliciumsubstraat.
De impact van een lage MRR op de productie-efficiëntie en -kosten:
Een lagere MRR resulteert in langere tijdrovende CMP-stappen van SiC-substraten, waardoor de verwerkingstijd en -kosten toenemen.
Zelfs als de bestaande CMP-methode gekwalificeerd 4H-SiC-substraat kan produceren, is een lage efficiëntie nog steeds het knelpunt dat de grootschalige toepassing ervan beperkt.
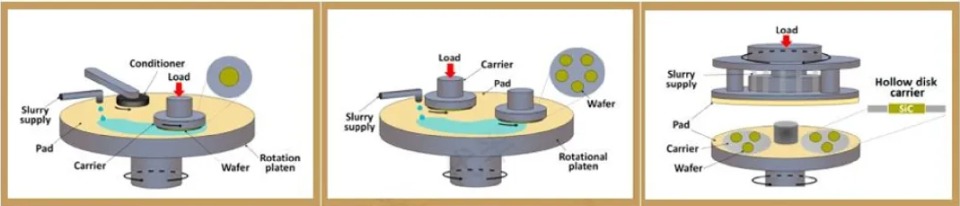
CMP-polijstproces
3. Technische vooruitgang om de CMP-efficiëntie te verbeteren:
Om de uitdaging van lage MRR aan te gaan, heeft de industrie dubbelzijdige, batch-polijsttechnologie ontwikkeld.
Deze geavanceerde technologieën hebben de manuren van CMP aanzienlijk teruggebracht, zoals de CMP-polijsttijd voor een enkele batch van 10 substraten van 3-5 uur naar 1 uur.
Dubbelzijdige polijsttechnologie verbetert niet alleen de efficiëntie, maar helpt ook de consistentie en vlakheid aan beide zijden van het substraat te behouden.
Samenvattend is de verbetering van de chemisch-mechanische polijstefficiëntie van siliciumcarbidesubstraat de sleutel om de brede toepassing ervan te bevorderen. Door de ontwikkeling van geavanceerde technologieën zoals dubbelzijdig polijsten en batchpolijsten wordt het probleem van de lage materiaalverwijderingssnelheid in het traditionele CMP-proces effectief opgelost, wordt de verwerkingstijd aanzienlijk verkort en worden de productiekosten verlaagd. In de toekomst, met de voortdurende verbetering van de prestatie-eisen voor SiC-materialen en de voortdurende innovatie van polijsttechnologie, hebben we reden om te geloven dat de voorbereiding van SiC-substraten efficiënter en economischer zal zijn, waardoor een solide basis wordt gelegd voor de verdere ontwikkeling van elektrische apparaten. Daarom zal de voortdurende verkenning en optimalisatie van het CMP-proces een belangrijke manier zijn om de brede toepassing van SiC-materialen op het gebied van halfgeleiders te bevorderen.