Aluminiumnitride-keramiek is een belangrijk warmtedissipatiesubstraatmateriaal, maar het aluminiumnitride-keramische substraat zelf heeft geen elektrische geleidbaarheid, dus het oppervlak moet worden gemetalliseerd voordat het wordt gebruikt als een krachtig warmtedissipatiesubstraat.
Het bevochtigingsvermogen van metaal op een keramisch oppervlak bij hoge temperaturen bepaalt de bindkracht tussen metaal en keramiek, en een goede bindkracht is een belangrijke garantie voor de stabiliteit van de verpakkingsprestaties. Daarom is de realisatie van metallisatie van keramisch substraat een belangrijk onderdeel van de praktische toepassing van aluminiumnitride-keramiek.
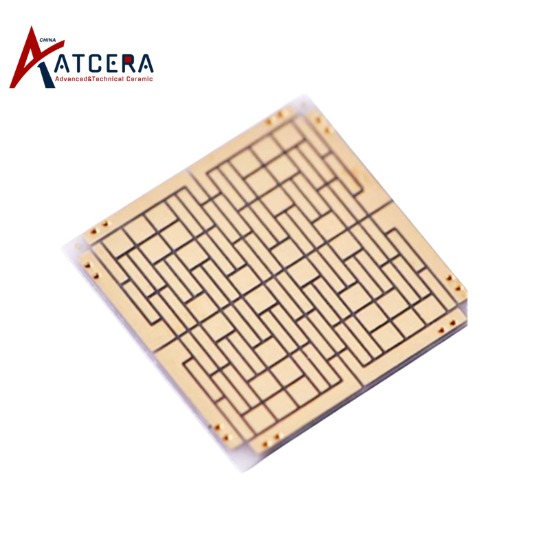
Mechanische verbinding en hechting
De mechanische verbindingsmethode wordt gekenmerkt door het aannemen van een redelijk structureel ontwerp en het gebruiken van mechanische spanning om de verbinding tussen aluminiumnitridesubstraat en metaal te realiseren, zoals hete mouwverbinding en boutverbinding. De mechanische verbindingsmethode heeft de kenmerken van een eenvoudig proces en goede haalbaarheid, maar de spanning bij de verbinding is groot, is niet geschikt voor omgevingen met hoge temperaturen en het toepassingsbereik is beperkt.
Binding verwijst naar het organische bindmiddel als verbindingsmedium, via het juiste hechtingsproces, de aard van het aluminiumnitridesubstraat en metalen materialen gecombineerd tot een mechanische gehele verbindingsmethode. De hechtmethode is echter ook niet geschikt voor omgevingen met hoge temperaturen en hoge sterkte, en het gebruiksbereik is klein.
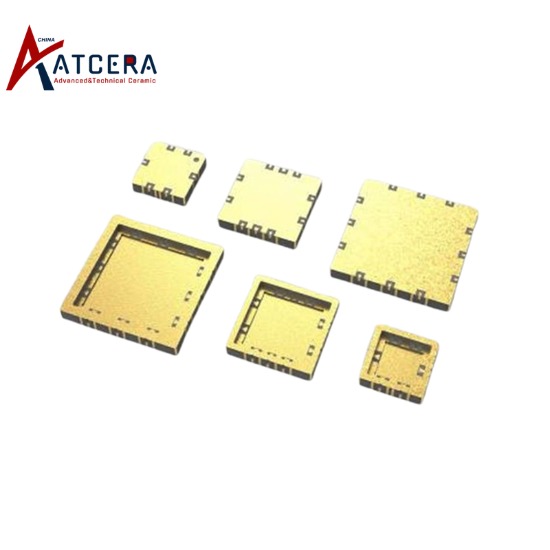
Dikkefilmmethode (TPC)
Dikke-filmmethode verwijst naar het proces waarbij een geleidende pasta rechtstreeks op het oppervlak van een keramisch aluminiumnitride-substraat wordt aangebracht door middel van zeefdruk, en vervolgens wordt gedroogd en gesinterd bij hoge temperatuur om de metaalcoating aan het oppervlak van het keramische substraat te laten hechten.
Geleidende pasta bestaat over het algemeen uit geleidend metaalpoeder, glasbindmiddel en organische drager. Het geleidende metaalpoeder bepaalt de elektrische en mechanische eigenschappen van de pasta na filmvorming, en de algemeen gebruikte metaalpoeders zijn zilver, koper, nikkel en aluminium, enz., Waarvan zilver en koper een lage weerstand en lage kosten hebben, en meer geschikt voor industriële productie.
Daarom is het proces betrouwbaar en heeft het de voordelen van een hoge productie-efficiëntie, lage kosten en een flexibel ontwerp. Het nadeel is dat het wordt beperkt door de precisie van het zeefdrukproces, dat de hechting niet gemakkelijk te controleren is en dat het gesinterde substraat geen hoge precisielijnen kan verkrijgen, dus het kan alleen worden toegepast op verpakkingsmaterialen voor elektronische apparaten met een lage lijn. nauwkeurigheidseisen.
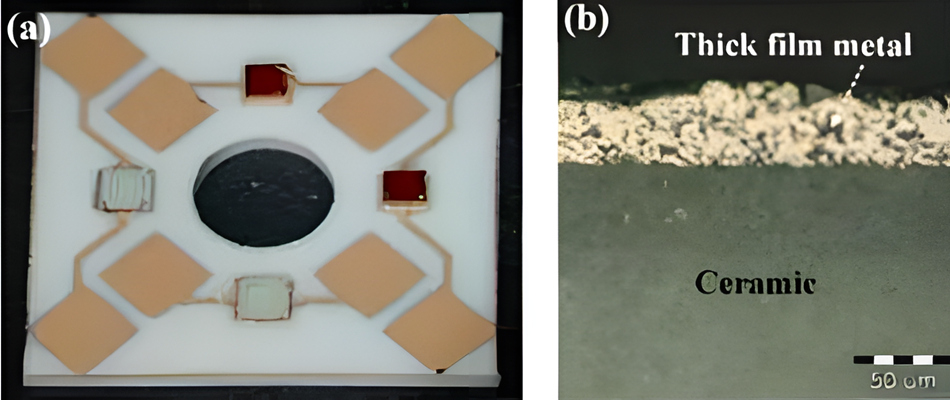
Actief metaalsolderen (AMB)
De actieve metaalhardsoldeermethode bestaat uit het direct toevoegen van Ti, Zr, Al, Nb, V en andere overgangselementen met relatief actieve chemische eigenschappen aan het gewone hardsoldeermetaal. Deze actieve elementen reageren direct chemisch met het oppervlak van aluminiumnitride-keramiek om een overgangslaag te vormen. Het belangrijkste product van de overgangslaag bestaat uit enkele metaalbindende verbindingen en heeft dezelfde structuur als het metaal, zodat het kan worden bevochtigd door het gesmolten vulmiddel metaal om een metallurgische verbinding te vormen.
Keramisch substraat van aluminiumnitride is een belangrijk warmteafvoerapparaat en wordt vaak gebruikt bij hoge temperaturen, dus er zijn meer verbindingen met hoge temperaturen nodig. Het actieve soldeermetaal op hoge temperatuur, voornamelijk bestaande uit CuTi en NiTi, kan worden gebruikt in het bereik van 1200 ~ 1800 ℃. Ternair systeem of multicomponent-systeem soldeermetaal vertegenwoordigd door Au-basis, Co-basis en PD-basis hardsoldeermetaal is het meest gebruikte actieve soldeermetaal bij hoge temperaturen. Het smeltpunt van Au, Co en Pd is respectievelijk 1064℃, 1492℃ en 1554℃, wat een rol speelt bij het verhogen van het smeltpunt in hardsoldeermetaal.
Omdat de actieve elementen in het soldeermetaal chemisch actief zijn, moet actief hardsolderen worden uitgevoerd onder bescherming van een ruwe vacuümomgeving of een inerte atmosfeer, om chemische reacties met zuurstof bij hoge temperaturen te voorkomen, en de technische kosten zijn hoog , en het is niet geschikt voor grootschalige toepassingen.
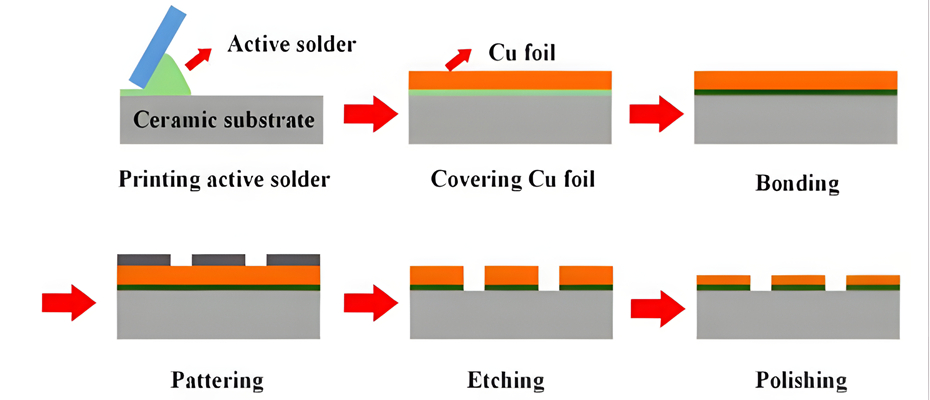